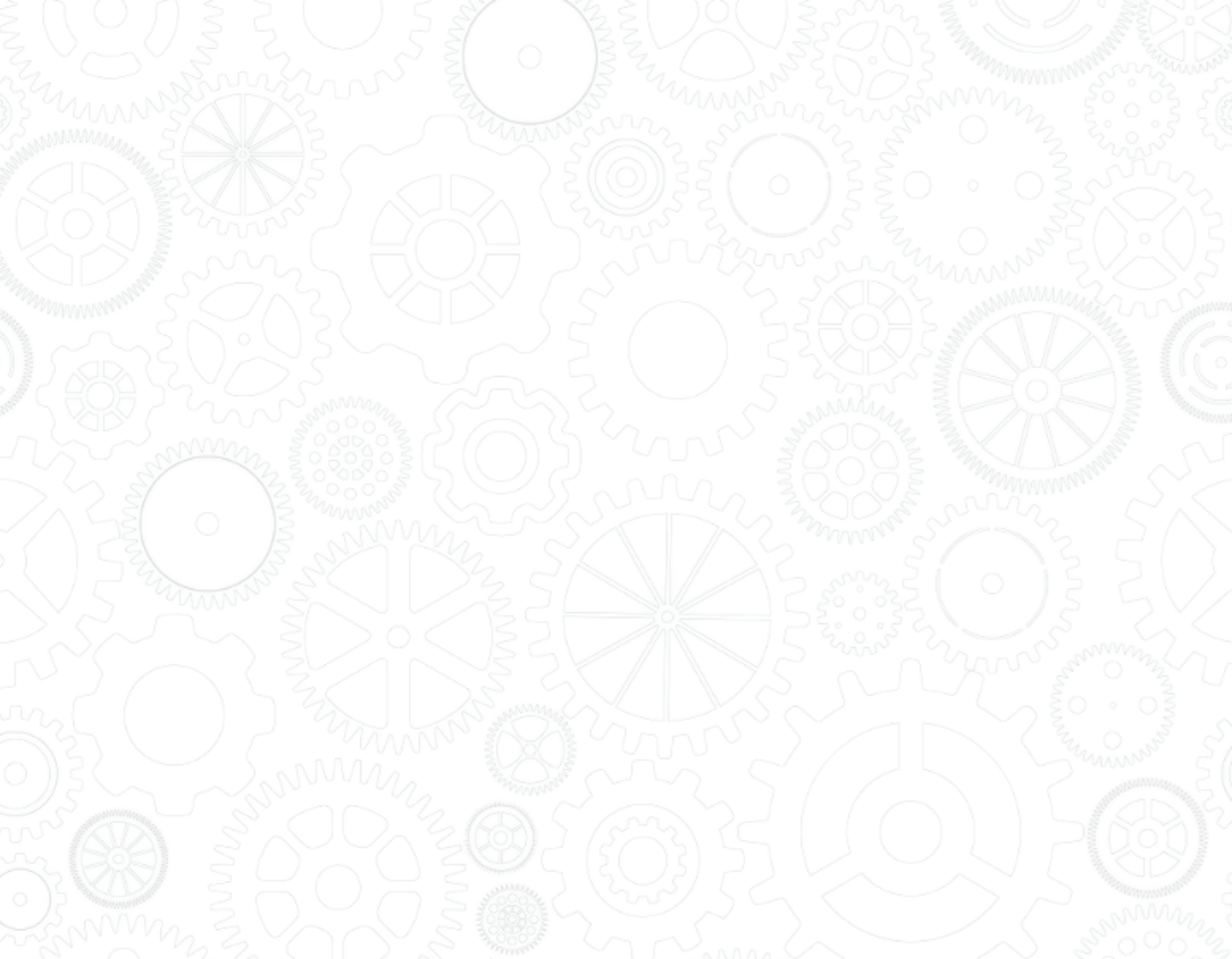
Steel Production Transformed: Where AI Meets Excellence
Experience the power of cutting-edge AI and ML technologies, reshaping steel manufacturing like never before.
Unleashing Next-Level Performance
Harness the full potential of data to conquer production challenges:
Mechanical Property Prediction: Achieve pinpoint accuracy in forecasting properties critical to performance.
Process Optimization: Streamline every step, driving efficiency to its peak.
Big Data Integration: Make sense of massive datasets, turning complexity into clarity.
AI-Driven Data Insights: Discover hidden patterns that unlock smarter strategies for success.
AI at the Helm of Innovation
Steel-Specific Precision: Tailored models to capture microstructure variability across steel types.
Trustworthy Predictions: Advanced techniques tackle overfitting and validate results on real-world datasets.
Transparency in Action: ML decisions demystified for engineers, bridging the gap between AI insights and practical implementation.
Unmatched Business Impact
AI/ML doesn’t just improve steel production—it revolutionizes it:
Cost Reduction: Drastically reduce scrap rates and rework by anticipating defects like cracks and impurities.
Real-Time Quality Assurance: Instantly identify deviations in vital parameters, ensuring top-notch output.
Scalable Solutions: Expand across production lines and steel types, simplifying processes while amplifying results.
Strength in Precision: Over 95% accuracy in predicting tensile strength—because excellence is no longer optional.
This isn’t just innovation—it’s transformation. With AI-driven solutions, steel production evolves into a realm of efficiency, reliability, and quality that drives exceptional business growth. The future is forged with intelligence—are you ready to lead the charge?
The Problem:
Did you know? The pharmaceutical industry loses nearly $50 billion annually [1] due to inefficient manufacturing processes. In the medical device sector, $26–$36 billion is wasted each year on direct costs like scrap and rework [2]—equivalent to a staggering 6.8–9.4% of total sales ($455 billion in 2022). These inefficiencies hinder growth, profitability, and trust.
And the semiconductor industry? One manufacturer alone reports $68 million in losses annually from yield losses across just eight production steps [3]. The good news? A mere 10% improvement in yield could save over $12 million annually per manufacturer. Imagine the transformative savings if applied industry-wide.
The Hidden Costs of Yield Loss
Financial: Rising scrap expenses, high maintenance costs, and lost revenue.
Operational: Bottlenecks, reduced throughput, and strained customer confidence.
Environmental: Unnecessary waste and excessive resource use.
Taking Action: Proven Solutions to Combat Yield Loss
Root Cause Analysis: Pinpoint defects with cutting-edge RCA techniques.
Statistical Process Control (SPC): Leverage real-time monitoring for precision.
Supplier Collaboration: Elevate standards with high-quality raw materials.
Standardization: Minimize variability during startup and transitions.
Preventive Maintenance: Ensure optimal equipment performance to prevent defects.
Common Root Causes
Yield losses often stem from:
Equipment malfunctions.
Human errors.
Substandard materials.
Process Deviation
By addressing these challenges, industries can unlock untapped savings, strengthen trust, and reduce environmental impact. It's time to seize the opportunity—drive efficiency and take control of the future.
References
[1] S.Neuman, Pharmaceutical industry wastes $50 billion a year due to inefficient manufacturing, The Source, Washington University Journal, October 9, 2006.
[2] A. Melnyk and A.Artsen, Supporting Device Reprocessing To Reduce Waste In Health Care, Federation of American Scientists, February 10, 2025.
[3] K.D.Backer, R.J.Huang, M.Lertchaitawee, M.Mancini and C.L.Tan, Taking the next leap forward in semiconductor yield improvement, Advanced Industry Practice, Mckinsey & Company Report, April 2018.
Turning Obstacles into Opportunities
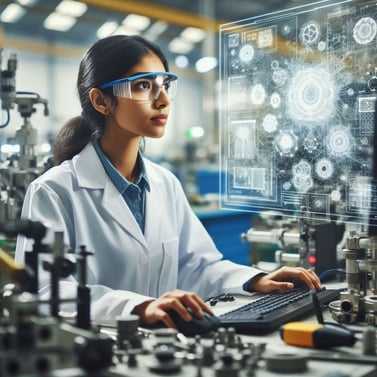
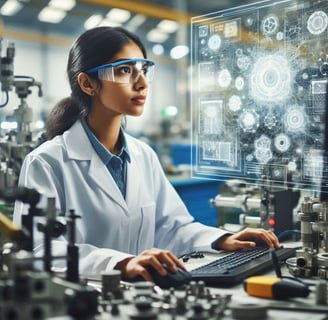